BUS
- HOME
- BUSINESS
- BUS
Our Bus Products Business has the largest market share in Japan for resin molded outer plate components used in large-sized tourist buses. Using advanced production technology, we provide high value-added products offering reliable quality, safety and functionality. Our product lineup includes such molded components as front panel, rear panel, bumper, and upper/lower company name lights. Also we manufacture cooler/heater ducts and chassis pipes, assemble driver guards, and install accessories. We deliver glass assemblies for large buses on a just-in-time basis, helping to improve the productivity of bus manufacturers. In addition, we perform outfitting and mounting work, including installation of luxury restrooms or wheelchair lifts (for welfare buses). Taking advantage of the know-how and techniques accumulated through the bus products business, we are also working on manufacturing of seat covers for the Shinkansen and tire covers designed to reduce the weight of trucks. We will continue to refine our molding techniques and technology to meet new demand.
Exterior and interior parts
Manufacturing / processing / assembly
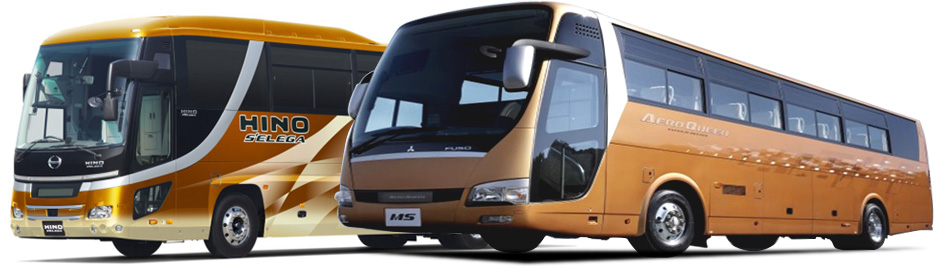
Production parts lineup
- front panel
- Rear panel
- Front center bumper upper
- Front center bumper lower
- Bus step
- Company light
(Glass / PC mounting)
- Company light upper
- Cooler, heater duct processing
- Driver guard installation
- Accessory mounting
- Large bus rear luxury dressing room
- Wheelchair accessible lift with welfare bus
- Electrical components
Hand Lay-UP molding
- Hand lay-up molding is a process to manually laminate glass mats to molds to a specific thickness. This process is suitable for large-variety small-volume production, and enables complex-shape and/or large-size molding. The front and rear panels and bumpers of large sightseeing buses are manufactured by this method.
"Hand lay-up molded components" production flow chart
- [1] Molding process
- The glass mats are laminated to the specified thickness by hand. In order to improve strength, unique know-how such as partial use of reinforcements is employed.
- [2] Trimming process
- This process is for cutting the molded components to specified dimensions. Simple shapes are processed by robotic systems, such as a trimming machine, while complicated shape trimming is performed manually.
- [3] Setup process
- Necessary fixtures are attached to the cut components. This operation is performed by hand.
- [4] Polishing process
- The surface of the molded components set on the fixture is polished until it becomes a beautiful surface.
- [5] Painting process
- The polished mold components are painted.
- [6] Inspection process
- It is checked whether there is any scratch, dent or hole on the surface of the painted mold components.
- [7] Finishing process
- Defects found in the inspection process, if any, are corrected.
- [8] Delivery
- The finished components are delivered to the bus manufacturer.
Various parts production and processing
- Machining center
- Turning center
- Pipe processing
- Pipe welding